TPM (Total Productive Maintenance)
TPM, die Totale Produktive Instandhaltung, ist eine Methode zur ständigen Verbesserung der gesamten Effektivität der Betriebsanlagen. TPM erfolgt unter der aktiven Beteiligung aller Mitarbeiter.
Eine „gelebte“ TPM-Kultur bewirkt die konsequente Beseitigung möglicher Verlustquellen in der Produktion und vermeidet somit unnötige Verschwendung. Ein großer Bestandteil der Verbesserungen durch TPM besteht in der Reduzierung von ungeplanten Maschinenstillständen, der Vermeidung von Leerlauf und Mikrostillständen sowie der Minimierung von Rüstzeiten und Werkzeugwechseln.
Es gibt unterschiedliche Ansätze und Definitionen bezüglich der TPM Organisation. Meist wird die gesamte TPM Methode als Säulenmodell mit 4 bis 8 Säulen dargestellt. Wir empfehlen – gerade zu Beginn – mit dem kompakten 4 Säulenmodell zu starten. Das 4 Säulenmodell beinhaltet die wesentlichsten und gleichzeitig wirksamsten TPM-Elemente.
Das TPM Säulenmodell:
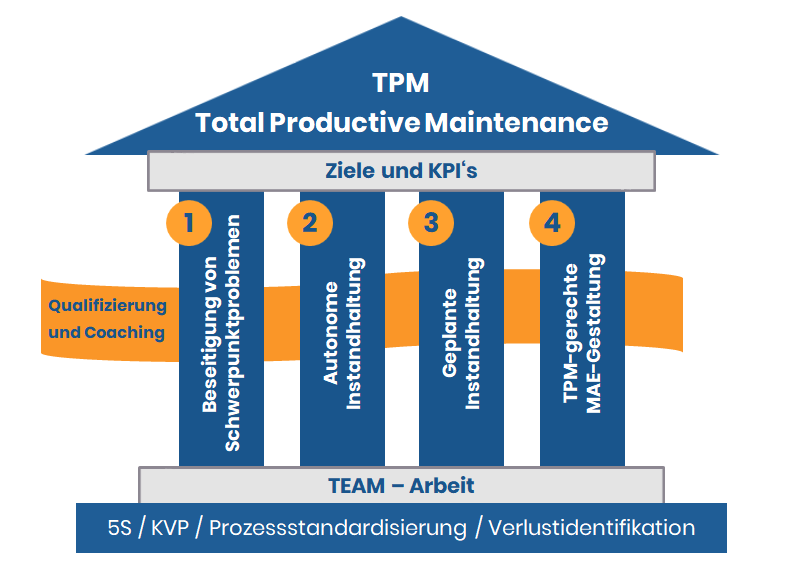
5S, KVP und Prozessstandardisierung bilden die Basis für TPM. Das Verständnis für „Wertschöpfung“ und die Identifikation von Verlusten ist ebenfalls unerlässlich. Ein solides Fundament, klare Zielsetzungen und Teamarbeit bilden die Grundlage dafür, TPM erfolgreich im Unternehmen zu etablieren.
Die Inhalte der einzelnen Säulen bilden den Kern der TPM Entfaltung:
1. Beseitigung von Schwerpunktproblemen
Das Bedienpersonal ist im Sinne der ständigen Verbesserung in der Lage, auftretende Störungen zu analysieren, Ursachen zu identifizieren und diese nachhaltig zu beseitigen.
2. Autonome Instandhaltung
Alle routinemäßigen Aktivitäten zur Anlageninstandhaltung (Wartung und Instandsetzung) werden im Rahmen der Teamarbeit vom Bedienpersonal in Eigenverantwortung durchgeführt.
3. Geplante Instandhaltung
Durch weiterführende Instandhaltungsmaßnahmen werden die Anlagen und Einrichtungen so “in Schuss” gehalten, dass keine ungeplanten Stillstände auftreten und sich die Lebenslaufzeit der Anlagen und Einrichtungen wesentlich erhöht.
4. TPM-gerechte MAE-Gestaltung
Die Erkenntnisse und Maßnahmen aus den ersten Säulen bezüglich Instandhaltbarkeit, Zugänglichkeit und Bedienungsfreundlichkeit der Anlagen und Einrichtungen, werden bereits in der Planungsphase und Beschaffungsphase neuer Anlagen berücksichtigt.
Die folgenden Faktoren zeichnen ein erfolgreich etabliertes TPM aus:
- Steigerung der Gesamtproduktivität
- Senkung der Anlagenverluste
- Einbeziehung aller Mitarbeiter durch konkrete Aufgabenstellung
- Wesentliche Erhöhung der Identifikation aller Mitarbeiter mit ihren Einrichtungen
- Verbesserung der Prozess- und Produktqualität
- Wesentliche Erhöhung der Lebenslaufzeit von Anlagen und Einrichtungen
- Planbare Wartung statt ungeplanter Maschinenausfälle
Mit TPM rücken die involvierten Akteure und Abteilungen wesentlich näher zusammen. Es entstehen leistungsfähige Teams, die den heutigen Anforderungen gewachsen sind. Durch TPM erreicht man eine flexible und planbare Produktion und Anlagenauslastung ohne permanente „Feuerwehreinsätze“.
Kontaktieren Sie uns
Benötigen Sie weitere Informationen zu dem Thema?
Nutzen Sie das Kontaktformular.
Wir informieren Sie gerne!